Next generation controller, RCA2500 with open network
(DeviceNet) used first in the industry to control a
huge number of input and output devices and communicate
with molding machines and auxiliaries.
Touch
panel interface
- Easy-to-see 6.5 in. color LCD
- Excellent grip feeling and key arrangement
- Jog dial for easy setup
- Two 3-position safety switches for safe operation
- Tool buttons for direct access to frequently used
functions
- User-friendly guidance and help
- A hundred mold setups memory in controller
- Setting keys and operation keys grouped and located
separately to avoid misoperation
- Optional off-line programming
- Conveyor counter
- Sampling counter
- Standard pendant holder. Pendant can be attached
to off-the-shelf stand. (in accordance with VESA standard)
- ROBOT OFF mode by selector switch. Individual operation
of molding machine is available without disconnection
of interface cable and inserting jumper plug.
- PAUSE (step stop) and QUICK PAUSE (instantaneous
stop) for flexible operation.
- Teach possible switch to inhibit unauthorized person
from going into program mode.
- Absolute servo system. ABS encoder of 17 bit bus
line prolongs battery life to 6 years under normal
working environment.
- Kanji translation to enter mold names.
- JOG switches for main arm and sub arm are separately
located on the pendant without the need of actuating
an arm selector switch.
- Step verification operation to confirm robot motions
by step and verification operation to confirm the
motions at actual speed before automatic operation.
- Twenty-eight motion items (4 items can be optionally
added.)
- Immediate stop with servo power off, if press door
or safety guard is open.
- Screen saver becomes active without any operation
for long period. Backlight off mode is also available.
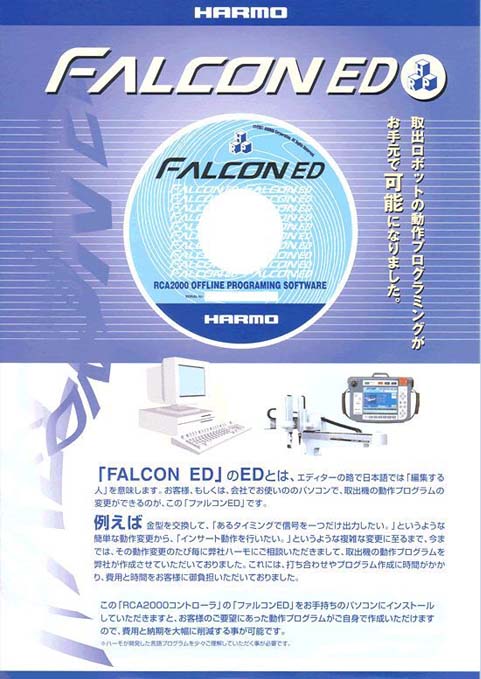 |